Model predictive control (MPC)
Original date of publish: Mon 10 Sep 2018 10:00:00 AM EEST
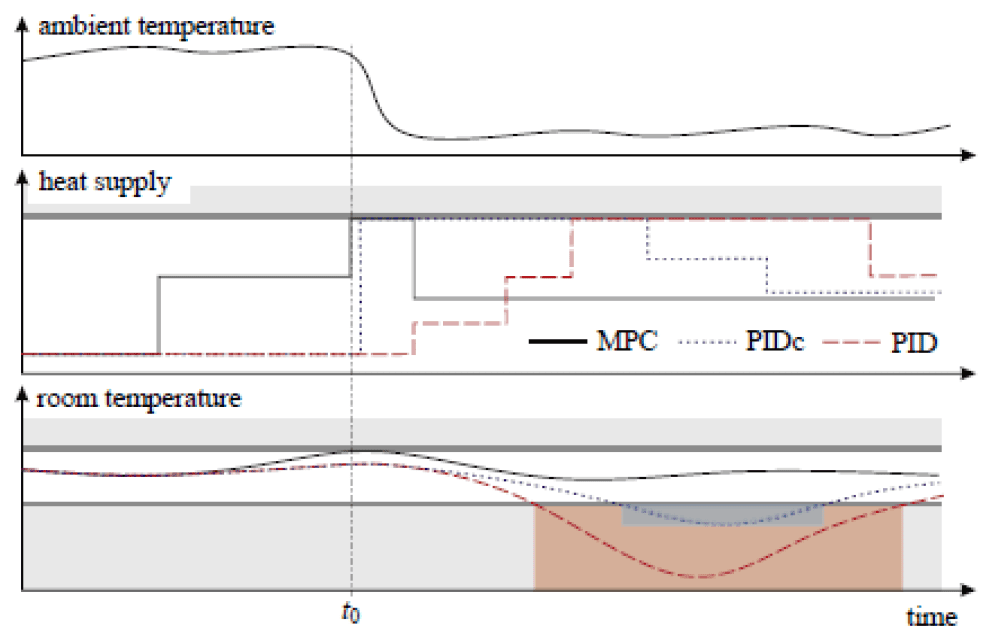
Main ideas of MPC
MPC uses an explicit linear or nonlinear model of the plant and knowledge of disturbances and setpoint changes for predicting future control errors. The controlled plant may be SISO (Single Input, Single Output) or MIMO (Multiple Input, Multiple Output). Additional advantage of MPC over traditional control methods is the ability to incorporate operating constraints, for example a minimum and maximum value of control input, in the control system design. [2]
In the context of building heating control, slightly different formulations of the cost function (6) are often used. These will be further discussed in Sections 4.5.4 and 4.6. For a linear (traditional) control model, (6) - (7) the predictive output control value is a quadratic optimization problem, for which several efficient solvers exist, for example Quadprog in MATLAB [3]. It can be noted that without the constraints (7), the calculated optimal control equals to that of the Linear Quadratic Regulator (LQR). [2]
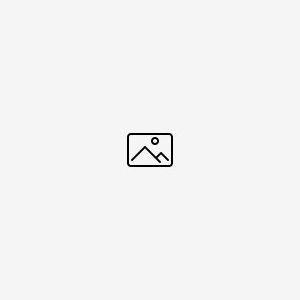
Figure 1: The heating load of the heating radiator on the right-hand side is significantly larger than the one on the left-hand side, causing discrepancies in the temperatures perceived by the occupants in the rooms.
Receding Horizon Control (RHC)
Although an optimal control input is obtained from (6) - (7) for time instants k + 1, k + 2, . . . , k + N, usually only the first control input is applied. When a new measurement arrives at time k + 1, another sequence of control inputs for time instants k +2, k +3, . . . , k +N +1 is obtained from the optimization algorithm. The principle in which only the first control input is applied, and the optimization is executed after every measurement, is referred to as the receding horizon control principle. It makes the optimal controller less sensitive to model inaccuracies and allows the derivation of analytical proofs of closed-loop stability, which are omitted here and not explained further.
Model Predictive Control (MPC) used in buildings
In building automation several factors suggest great potential of MPC over traditional control methods of HVAC systems. Buildings generally have slow dynamics due to insulation and large thermal mass, making it necessary to plan heating in advance (see figure 10). Knowledge of the main disturbances like ambient temperatures, solar radiation levels, room occupancy status are also readily available. Of special interest has been the use of MPC in electricity network load shifting, a key component in smart grids and demand response programs. MPC can also be used to integrate several independent systems cost-efficiently like heating, ventilation and air conditioning. [4]
Existing implementations of MPC in building heating
Some existing implementations of MPC in building heating control are briefly discussed next. The main findings, especially in terms of energy usage and implementational issues are summarized.
Case 1: Czech Technical University, Prague
MPC has been implemented for heating control in a building of the Czech Technical University (CTU) in Prague. The implementation of MPC reduced energy consumption of heating by 17-24% when compared to a weather-compensated controller.
The heating system used in the study (ceiling radiant heating system) is different from those usually available in Finland. In the study, Subspace Identification method was used to obtain the dynamic model of the heating system. The identification phase was two-fold: first an initial model was identified based on operational data. The initial model was later improved by specifically designed identification experiments conducted from late December to early January. Only predictions of ambient temperature were considered. The authors of the study report difficulties in obtaining the dynamic model as the main challenge of implementing MPC for buildings. [5]
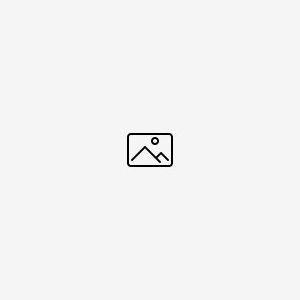
Figure 2: MPC is able to adjust heat supply proactively before a change in ambient temperature, yielding superior performance over standard PID-control and PID with external temperature compensation (PIDc) [4]
Case 2: OptiControl
Opticontrol [6] is an interdisciplinary research project on novel predictive control strategies for cost-efficient control of buildings’ HVAC-systems. In the Opticontrol project, an integration of all building automation systems was considered, i.e. in addition to heating also control of blinds, ventilation etc. was considered. The modelling method considered was based on RC-analogue models. The case building was a fairly new office building in Switzerland. No relative comparison of energy consumption was made, but the authors concluded that based on simulations, the MPC would reduce energy consumption by 17%, when compared to a rule-based controller. The authors concluded that for current energy prices the required effort, with respect to system identification and other engineering required for the deployment of MPC, is too high to justify its implementation for similar buildings. [7]
Summary of implementations
The table 1 summarizes the MPC implementations discussed above. The effect of MPC on energy consumption depends on the number of systems utilizing the MPC and the buildings’ physical properties (e.g. insulation). The use of MPC for integrating several systems may bring certain synergical advantages (for example, slight decrease in ventilation during a demand peak in heating).
The ability of MPC for load shifting is in itself important related to demand side management and smart grids. However, it can be concluded that MPC’s applicability for commercial products is inherently limited due to the need of sufficiently accurate dynamic models. For commercial, plug-and-play, types of systems sufficiently accurate models cannot be obtained solely based on historical data, and often lengthy system identification experiments cannot be carried out without sacrificing user comfort. For office buildings, scheduling the identification phase during Christmas holidays might be a viable option.
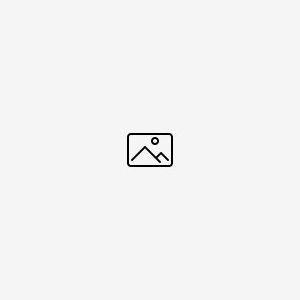
Table 1: Comparison of MPC implementations.
References: